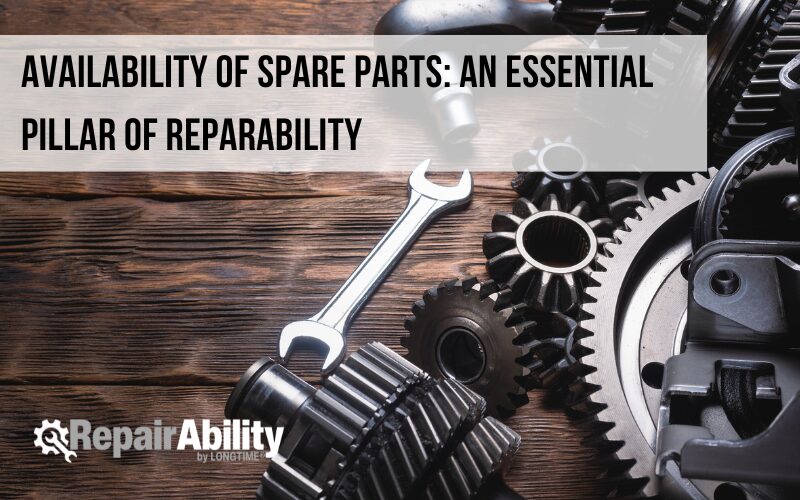
The availability of spare parts: an essential key to reparability
The availability of spare parts is a key factor in the repairability of products. As a manufacturer, you need to understand that the right to repair is increasingly recognised by legislation, and that legal obligations regarding the supply of spare parts are growing. Supplying spare parts is not just a question of compliance, but a commitment to respect reparability standards and to support your customers throughout the lifespan of your products.
The right to reparation and reparation legislation
The right to repair has been the subject of several pieces of legislation around the world, particularly in Europe. Indeed, the European Union imposes strict requirements to guarantee the long-term repairability of products. This includes making spare parts, technical manuals and repair guides available to professionals and even consumers. Compliance with these obligations is essential to avoid legal sanctions and maintain consumer confidence in your brand. The right to after-sales service must be respected, and this means guaranteeing access to the parts needed to repair your products.
Today, the Ecodesign Directive and its delegated regulations, followed by the ESPR and the Right to Repair Directive, make it clear that these issues will become increasingly important.
In addition to these supranational measures, many European countries are strengthening their legislation on the right to repair and consumer protection. For example, in recent years, France has introduced an article of law
‘Art. 25 Any technique, including software, by which a marketer seeks to make it impossible to repair or recondition an appliance outside its authorised channels is prohibited.
Any agreement or practice whose purpose is to limit access by a repair professional to spare parts, instructions for use, technical information or any other instrument, equipment or software enabling products to be repaired is prohibited.
This article is significant, and many market players are not yet in compliance with the law.
The importance of clear, transparent communication on parts availability
Above and beyond legal obligations, clear communication on the availability of spare parts is essential if you are to establish a relationship of trust with your customers. You need to inform your users about the accessibility of parts, how long they will be available and the support period after purchase. This transparency also includes providing a directory of compatible and alternative parts. Transparency of repair costs, including detailed quotations, ensures a satisfactory user experience, where the customer knows exactly what to expect in terms of costs and timescales.
Spare parts and delivery stock management
Another crucial aspect is stock management. It is essential to ensure that spare parts are available for a minimum period, which may or may not be stipulated by legislation. This includes long-term storage of essential parts. In addition, it is necessary to ensure that parts are delivered on time, with transparent communication on delivery times to avoid any consumer dissatisfaction.
But stock management can quickly become a constraint if it is under- or oversized. It is therefore very important to anticipate needs and demand, and in this respect, monitoring the reparability of products helps to optimise stock management.
Seller’s liability and remedies in the event of faulty repairs
If a spare part is missing or if the repair is not carried out correctly, you have a contractual responsibility to supply the part or to guarantee a legal remedy for the consumer under the legal conformity guarantee.
However, with the advent of the Right to Repair regulation mentioned above, this reparability obligation could extend well beyond the legal conformity guarantee.
Compliance with repair obligations is fundamental to avoiding legal disputes and ensuring customer satisfaction. In the event of failure to repair, it is your responsibility to propose appropriate legal remedies, thereby guaranteeing a quality after-sales service.
Impact of uptime on long-term repairability
The availability of spare parts has a direct impact on the long-term repairability of your products. A long-term parts stocking policy ensures that your products can be repaired for several years after purchase. This approach helps to reduce premature product obsolescence and enables your customers to keep their equipment in good working order, thereby reducing waste.
Conclusion: Supplying spare parts as a pillar of reparability
Supplying spare parts is not only a legal obligation, it is also an essential element in maintaining the repairability of your products. Not only does it ensure compliance with legislation, it also enables you to support your customers over the long term. Proactive management of spare parts, transparency about their availability and solid warranties enable you to reinforce your professional responsibility and remain competitive in a market that is increasingly focused on durability and repair.
1. What types of products require mandatory spare parts, and how does this impact the after-sales service strategy?
Products that require mandatory spare parts are mainly those that are designed to last several years and contain replaceable or reusable components. This includes household appliances, electronic equipment (such as computers and televisions), power tools and industrial products.
As part of an after-sales service (AS) strategy, it is essential to plan for the long-term supply of spare parts. This has an impact on stock management, logistics and resource planning. An effective strategy must include working with reliable suppliers, optimising supply processes and setting up approved repair centres capable of maintaining a fast, efficient service.
In addition, a commitment to a reparability policy means creating a support infrastructure to ensure the availability of parts for the life of the product, taking into account technical specifications and legal constraints.
2. How can we ensure the continuous availability of spare parts for the products concerned throughout their lifecycle?
Ensuring the continuous availability of spare parts requires proactive management and long-term planning. It is crucial to maintain appropriate stocks throughout the product life cycle. This includes accurately estimating demand for spare parts, particularly after the production phase, to anticipate future requirements.
Partnerships with spare parts suppliers are also a key factor. These partnerships should be based on long-term supply agreements and the possibility of reconditioning spare parts as part of a circular economy approach. Logistics and rapid parts replenishment need to be optimised, particularly for products with more irregular demand.
In addition, the management of product data and historical demand can provide crucial information for forecasting future spare parts requirements and avoiding stock-outs.
3. What are the legal regulations governing the availability of spare parts and how can compliance be ensured?
The legal regulations governing the availability of spare parts are mainly defined by the European directives on ecodesign, waste management and reparability. The Ecodesign Directive imposes obligations on manufacturers to make spare parts available for a specified period after sale, guaranteeing consumers access to repairs and spare parts for a period of 7 to 10 years for certain products.
Compliance with these requirements is essential to avoid legal penalties and guarantee consumer satisfaction. Compliance requires constant regulatory monitoring to keep abreast of changes in European directives and adapt internal practices accordingly. It also means keeping technical documents up to date, providing easy access to parts and guaranteeing transparency on costs and delivery times.
4. Quels avantages peuvent être tirés de l’utilisation de pièces détachées d’occasion dans une logique d’économie circulaire, et quels sont les risques ?
Using second-hand spare parts as part of a circular economy approach offers a number of ecological and economic advantages:
Reducing waste: Reusing parts that have already been produced limits the amount of electronic waste and the need to produce new parts, helping to reduce the ecological footprint of products.
Saving natural resources: Reusing parts reduces the consumption of natural resources for the production of new parts, thus conserving raw materials and preserving ecosystems.
Reduced costs: For manufacturers and consumers, the use of second-hand parts often reduces production and repair costs, making products more affordable and accessible.