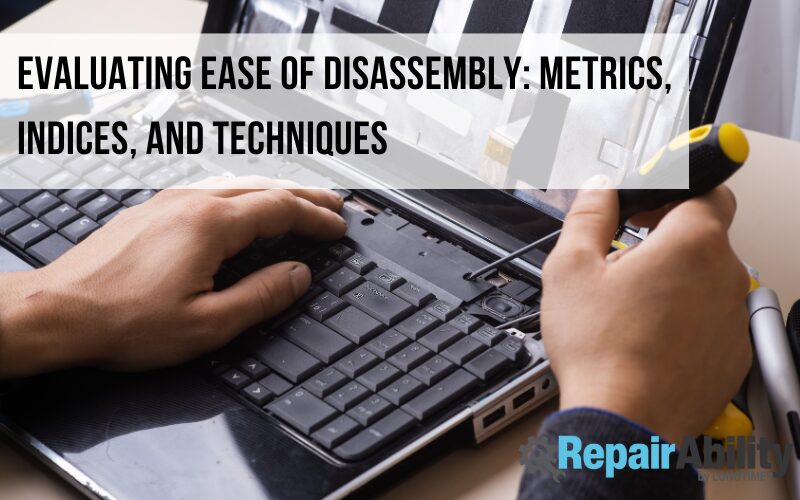
Assessing ease of disassembly: a key approach to reparability and eco-design
Extending product life and promoting a circular economy starts at the design stage.
In this article, we take you step-by-step through why and how to assess a product’s ease of disassembly.
Through precise technical criteria, recognized evaluation methods and best practices from the field, discover how to integrate dismantlability at the heart of your eco-design projects, for more sustainable, repairable and responsible products.
Assessing a product’s ease of disassembly is essential to improving its reparability and promoting sustainable design. This approach is fully in line with the principles of eco-design, aimed at minimizing the environmental impact of products throughout their lifecycle.
Why assess ease of disassembly?
Before attempting to measure or compare ease of disassembly, it is essential to understand what is at stake. This section explores the fundamental reasons why this approach is essential, both to extend product life and to meet new sustainability requirements.
A lever for repairability and durability
Ease of disassembly is a key factor in extending product life. By facilitating access to internal components, it becomes easier to replace or repair faulty parts, thus reducing the need to replace the whole product. This approach promotes a more efficient use of resources and reduces the production of electronic waste.
A key indicator for steering the circular economy
In a circular economy, the ability of a product to be easily dismantled conditions the efficient recovery of its components and materials.
Evaluating ease of disassembly enables us to identify the technical bottlenecks that hinder repair, reuse or recycling.
In this way, dismantlability becomes a strategic indicator for designing products capable of remaining in long value loops, limiting the consumption of virgin resources and the production of waste.
Facilitating reconditioning and remanufacturing
The ability to cleanly dismantle a product is a prerequisite for industrial processes such as reconditioning and remanufacturing.
These processes involve recovering used products, replacing defective components, bringing functional elements up to standard and putting a product back into circulation with near-new performance.
Assessing ease of disassembly enables us to identify technical obstacles that would limit the economic viability of remanufacturing, such as :
– complex access to critical parts,
– the use of irreversible fasteners,
– or the need for proprietary tooling.
In this way, disassembly is not only a lever for extending end-user life, but also a major vector for industrial circularity.
A criterion incorporated into standards and regulations
Standards such as EN 45554 and initiatives such as France’s reparability index incorporate ease of disassembly as an assessment criterion. These regulatory frameworks encourage manufacturers to design products that are more easily repairable, thus aligning industrial practices with sustainability objectives.le-sav.fr
What are the key criteria to analyze?
To assess the ease with which a product can be dismantled, precise technical criteria are required. This section reviews the main parameters to be observed in order to build a relevant, reliable and eco-design-oriented analysis.
Disassembly depth
Disassembly depth refers to the number of steps required to access a specific component within a product. The fewer the steps, the easier the disassembly.
Number and type of fasteners
The type (screws, clips, adhesives) and number of fasteners influence ease of disassembly. Standardized, reusable fasteners simplify the process, while specific or hidden fasteners can complicate it.
Tools required
The accessibility of the tools required for dismantling is crucial. Tools that are easily accessible to the public enable more end-users to repair their product. Common tools facilitate the process, while specialized tools can be an obstacle to repair.
Component accessibility
Component accessibility is crucial in a reparability approach. Closely linked to disassembly depth, it quantifies the ease of access to a component. For example, a screw hidden under an adhesive is a common practice that greatly reduces component accessibility.
Available technical documentation
The availability of detailed service manuals, technical diagrams and troubleshooting guides is essential to guide repairers through the disassembly and repair process.
Skill level required
A product designed to be repaired without advanced technical skills significantly increases its repairability potential. The skill level assessment can be classified from “novice” (intervention possible by a lambda user) to “manufacturer” (intervention reserved for qualified technicians trained by the manufacturer). By lowering the threshold of competence required, we encourage the democratization of repairs, particularly outside professional circuits.
The main metrics for measuring dismantlability
To analyze the ease with which a product can be disassembled, it is necessary to rely on clear, objective and comparable metrics. These indicators make it possible to identify the main points of complexity in a product, and guide design choices towards greater durability and reparability.
Number of disassembly steps
This metric counts the number of actions required to access a target component. The higher the number of steps, the more complex and potentially risky the disassembly. This approach is also used in some European standards frameworks, where the notion of disassembly depth is integrated as a repairability criterion.
Disassembly time
The time required to remove a component is a direct measure of dismantlability. Standardized methods, such as that used in the eDIM indicator, are based on time grids associated with the main disassembly operations, thus ensuring a reproducible and objective assessment.
Difficulty coefficients for fasteners and tools
To refine the analysis, some methods introduce coefficients weighting the difficulty according to :
- the type of fastener (standard screws, clips, adhesives, proprietary fasteners),
- and the type of tooling required (standard or specific tooling).
This approach better reflects the real effort required to dismantle a product, and enhances the value of designs that make it easier to work without special tools.
Methods for assessing ease of disassembly
Several methods have been developed over the years to objectively analyze the ease with which a product can be dismantled. These approaches make it possible to measure, compare and structure the assessment based on reliable technical criteria. This section presents the main methods recognized today to guide the design of more durable and repairable products.
Reference methods
eDIM (Ease of Disassembly Metric)
Today, eDIM is the main index used to assess a product’s ease of disassembly.
Developed to meet European standardization requirements, it is based on a structured analysis of disassembly operations, expressed in standardized units of time. The eDIM is based on the analysis of disassembly sequences in six task categories (tool change, connector identification, handling, positioning, disconnection and component removal).
It enables objective aggregation of the effort required for complete or partial disassembly of a product, and offers an ideal balance between precision and ease of use.
The MOST method (Maynard Operation Sequence Technique)
The MOST method is the work analysis technique used to build the eDIM.
It is based on the modeling of elementary human operations in the form of standardized sequences (horizontal and vertical movements, inputs, placements, etc.).
MOST makes it possible to accurately and reproducibly calculate the time required to perform each dismantling task, while remaining accessible for industrial and regulatory applications.
Today, it is widely recognized as the basic method for constructing reliable dismantling indices.
Complementary methods
The U-effort method
The U-effort method calculates an effort index for unlocking fasteners, based on their physical properties (size, type, force required).
While it is relevant for assessing the difficulty of disconnecting a specific connector, it is limited in that it does not include all the operations required for complete disassembly (identification, handling, etc.).
The U-effort method can therefore be used as a complement for very detailed analyses, but is not a sufficient approach on its own.
Several older methods have contributed to our understanding of disassembly:
- Philips ECC method: based on databases of dismantling times measured for certain product families.
- Desai & Mital method: incorporates various factors influencing dismantling, but does not cover all preparatory tasks.
- The Kroll method: very detailed, using subjective difficulty categories.
While these methods have enabled significant progress to be made, they now have their limitations when it comes to standardized, regulatory application. They are therefore mainly cited for historical purposes.
Towards an operational evaluation method
Selection of priority parts
Selection of priority parts
Identifying the critical components to be assessed is a key step. These are generally the parts most prone to wear or failure. These items should be selected on the basis of their functional importance and replacement frequency.
Weighting criteria and calculating a score
Each criterion can be weighted according to its impact on reparability. For example, the accessibility of a component will be given greater weight than the shape of its screws. Aggregating these criteria generates an overall demountability score, which can be used for comparison purposes.
Aggregation of results and interpretation
Once the criteria have been evaluated, the results are aggregated into a demonstrability index. This score can be used to identify areas for improvement and guide decisions during the product design or redesign phase.
Best practices and feedback
Feedback from committed manufacturers
Manufacturers who have integrated reparability into their design processes are reporting multiple benefits: reduced after-sales costs, customer loyalty, alignment with regulatory obligations. This feedback confirms the strategic importance of reparability.
Design examples to facilitate disassembly
- Standardized fasteners (Phillips screws)
- Reduced number of fasteners
- Modular design
- Elimination of permanent adhesives
These practices can easily be transposed to various sectors, and have a direct impact on repairability scores.
Common mistakes to avoid
- Use of non-reversible glue or solder
- Multiplication of proprietary fasteners
- Absent or incomplete documentation
- Hard-to-reach or unidentifiable components
These errors compromise not only repairability, but also the perception of lasting product quality.
Integrate ease of disassembly into your eco-design projects
Feedback from the field shows that ease of disassembly is a concrete lever for improving product durability. Let’s take a look at how to systematically integrate this requirement right from the design phase, using proven practices and tools.
Designing for easy disassembly
Integrating ease of disassembly right from the design phase is no longer an option: it’s a strategic lever for extending product life, reducing their environmental footprint and meeting regulatory and market expectations.
To maximize the impact of your approach, it is essential to:
- Anticipate disassembly right from the design stage, by limiting the depth of access and favoring simple, reversible assemblies;
- Standardize the fasteners and tools used, favoring reusable systems accessible with common tools;
- Carefully document disassembly and repair operations, to make interventions possible by a wide audience;
- Systematically assess ease of disassembly using recognized tools (eDIM, MOST) to guide your design choices and improve your reparability scores;
- Promote compatibility with reconditioning and remanufacturing, to extend the value of products within the circular economy.
By applying these best practices, you not only optimize the repairability of your products, but also pave the way for new, more sustainable business models based on reuse, reconditioning and long-term customer loyalty.
Find out more: Repair-ability.eu
Repair-ability.eu is the reference platform dedicated to assessing the reparability and dismantlability of electrical and electronic products.
You will find :
- standardized assessment methodologies,
- practical guides for integrating reparability right from the design phase,
- criteria grids adapted to different product types,
- as well as resources and feedback for improving equipment durability.
👉 Visit Repair-ability.eu to access tools, reference systems and news on reparability and the circular economy.
Further tools and resources
Main resources :
- Repair-ability.eu: your reference platform for access to repairability and dismantlability assessment methodologies, criteria grids by product type, and practical sustainability-oriented eco-design guides.
European standards :
- EN 45554: assessment of reparability, reuse and refurbishment.
- EN 45552: assessment of functional durability.
- EN 45553: assessment of remanufacturability.
Metrics and methods :
- eDIM (Ease of Disassembly Metric), based on the MOST method.
- French reparability index (evaluation grids by product category).
Other guides and collaborative platforms:
- iFixit Pro: community disassembly guides and repairer feedback.
- Circular Design Toolkit, TechForGood: circular eco-design tools from European initiatives.
Explore our practical resources!
Would you like to go further in assessing reparability and designing sustainable products?
Discover all our methodologies, tools and guides in free access on :
👉 Access Repair-ability.eu resources
Conclusion
Assessing ease of disassembly is an essential step in designing products that are more sustainable, repairable and compatible with the circular economy.
By integrating this requirement right from the design stage and relying on proven methods, manufacturers reinforce the value of their products while meeting new regulatory and environmental expectations.