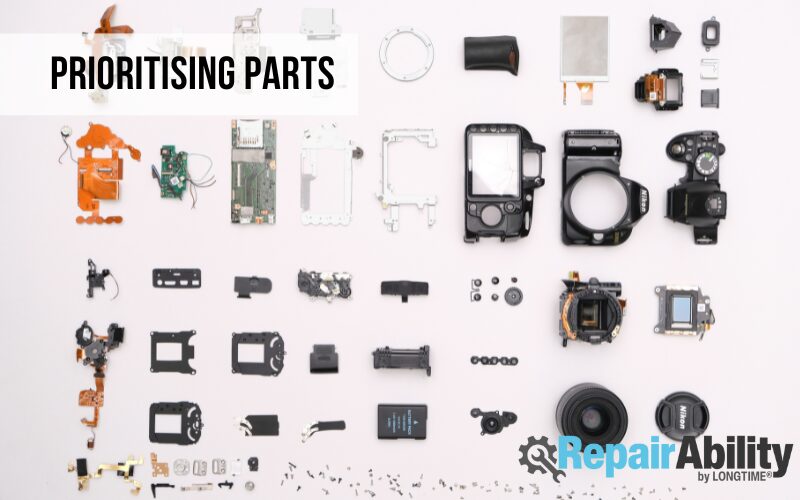
Prioritising parts: methodology and selection criteria
This article explores the criteria and methodologies used to classify parts according to their importance for repair, highlighting best practice and the assessment tools used by manufacturers and industry professionals.
What is a priority part?
A priority part is a component that is essential to the correct operation of a product, and whose shortage or unavailability compromises reparability. They are generally defined according to their impact on product performance and safety. It must be possible to replace such a part without requiring too much technical expertise or specific tooling, which is difficult for the general public to access.
What are the differences between priority parts and vulnerable parts?
Vulnerable parts are priority parts that are subject to a high user accidental breakage rate. For example, in a smartphone, the motherboard is a priority part, while the screen is a vulnerable part, because it needs to be replaced frequently and this is crucial to the product’s lifespan. Similarly, in a washing machine, the drum seal is a vulnerable part, while the drum is a priority part.
What are the differences between critical and priority parts?
Priority parts are defined as part of the reparability assessment, according to their failure rate and their functional role in the product. They are weighted and only those with a significant impact are included in the calculation of the score. Critical parts, on the other hand, are defined by regulatory texts to guarantee their availability for durability purposes. They are not weighted and are the result of legal obligations imposed on manufacturers. The same part can be both critical and priority, but the objectives are different: assessment on the one hand, regulatory requirement on the other.
Difference between priority and non-priority parts
Non-priority parts are replaceable without any major impact on the functionality or lifespan of the product. These are often cosmetic or accessory parts, such as protective covers, secondary buttons or plastic covers. Although their replacement may improve the product’s appearance or ease of use, it does not directly affect its ability to function.
Importance of priority parts in the reparability of a product
Having priority parts that are accessible and replaceable promotes a circular economy and reduces waste. Good parts availability also ensures rapid repair and limits programmed obsolescence. By incorporating easily replaceable parts into product design, manufacturers not only reduce the volume of e-waste, but also support customer trust and loyalty.
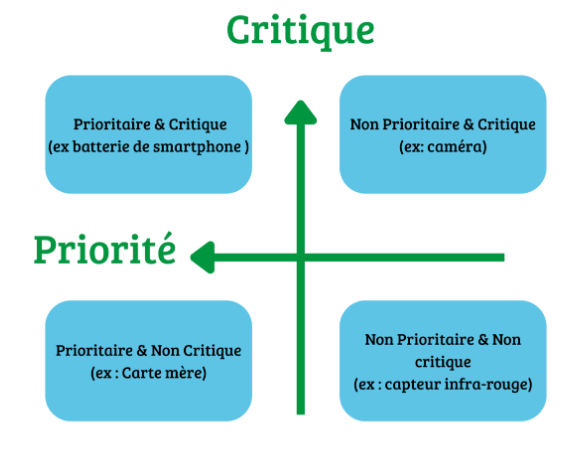
How do you identify priority parts?
Assessing the importance of parts according to the criticality of their role
A product is analysed according to the dependence of its essential functions on certain parts. This assessment is based on reliability studies and feedback from users and repairers. The more essential a part is for the product to function properly, and the more its failure results in the product being taken out of service immediately, the more critical it will be, and therefore the higher its priority.
Analysis of common faults and frequent points of failure
By analysing the failure rates for a series of products, we can identify the most vulnerable components and forecast the potential need for spare parts. Manufacturers can use after-sales service databases to identify recurring breakdowns and prioritise the supply of the parts most prone to failure.
Availability and ease of supply of spare parts
The accessibility of the components to be replaced has a major influence on repairability and must be fully integrated into the component hierarchy. Discontinued production or supply disruptions can make repairs impossible. A good practice is to favour open standards and the use of standardised parts to avoid dependence on a single production line.
Weighting process for priority parts
An analysis grid incorporates criticality, failure frequency and component availability. Quantitative methods, such as FMECA analysis, can be used to objectify these criteria. This analysis enables the components of a product to be classified according to their criticality in the event of failure, thus guaranteeing better management of stocks and supplies.
Tools and methods for assessing priority parts
Repairability analysis methods
FMEA: Failure Mode, Effect and Criticality Analysis
This tool identifies failure modes and their impact on the product. It enables us to anticipate repair needs and steer the design towards sustainable solutions. This method is widely used in mass production to improve the quality of products sold.
Tools for monitoring breakdowns and repairs
Maintenance data can be used to optimize the identification of critical parts. Computer-assisted maintenance management software (CMMS) makes this task easier. They enable breakdown trends to be monitored and spare parts stocks to be adapted accordingly.
Conclusion
Summary of key points for prioritizing parts
Optimizing reparability is based on a detailed analysis of the components essential to the product’s operation. Correct classification of priority parts promotes better resource management and reduced maintenance costs.
The importance of reparability for the circular economy
Appropriate management of priority parts reduces the environmental footprint and encourages responsible consumption. It prolongs product life and limits the production of electronic waste, while enhancing consumer satisfaction.
Impact of prioritization on sustainability and product lifecycle management
Better organization of parts helps extend product life and ecological efficiency. A proactive approach to the classification of priority parts enables manufacturers to have an overview of the different impact categories of their product, and to adapt to new regulations and growing expectations in terms of repairability and durability.