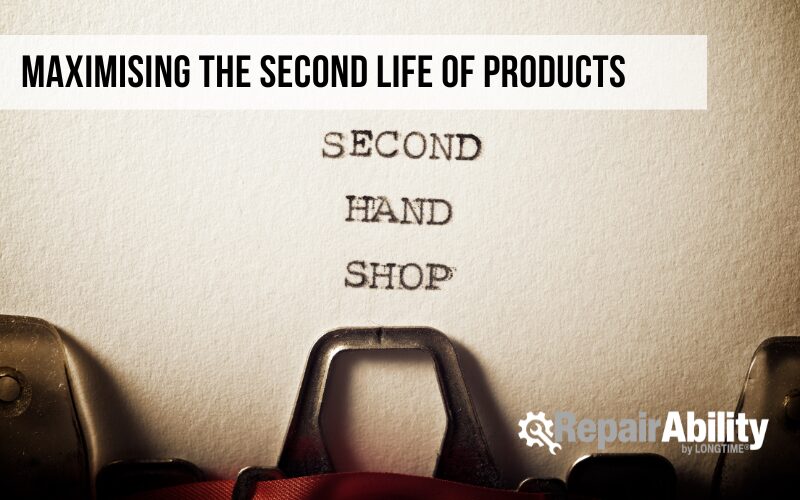
Maximising the second life of products: a major strategic lever
Increasingly concerned about the environment, companies that succeed in maximising the second life of their products position themselves not only as responsible players, but also as market leaders. By extending the life cycle of their products, they are responding to major environmental challenges while at the same time creating a competitive advantage. This process becomes a key differentiating factor, while offering the potential for long-term cost reductions.
Reconditioning: A systemic approach to industrial regeneration
Reconditioning is much more than a simple repair. It is a methodological industrial process that aims to fully restore a product’s functional capabilities by following a series of steps:
- Diagnosing the product: The process begins with an in-depth diagnosis, using advanced diagnostic tools to assess the precise state of the product.
- Repair and restoration: Next, a targeted technical intervention is carried out, incorporating cutting-edge repair solutions. These solutions include additive manufacturing, such as 3D printing to create precision parts, as well as molecular repair technologies for certain materials.
- Cleaning and aesthetics: The product is thoroughly cleaned and certain cosmetic parts can be changed to restore the product’s attractive appearance.
- Updating: Finally, logistics optimisation plays a key role, with strategic management of spare parts stocks, where algorithmic systems are used to minimise costs while maximising the availability of necessary components.
The residual value of products is inevitably a factor in the decision to recondition equipment. But for the process to work, the product must have a good level of repairability to make the process possible.
Repairability: a strategic performance indicator
Repairability has become an essential criterion for assessing industrial performance. Companies use standardised scores to measure how easy it is to repair a product. These scores are based on several criteria, including the accessibility of internal components, the availability of spare parts and the cost of repair compared with the cost of replacement. These indicators are essential not only to guarantee the durability of products, but also to ensure informed decision-making by consumers and businesses.
Reuse and recycling: a scientific approach to resource recovery
Modern engineering emphasises reuse right from the design phase.
The guiding principles of this approach include structural modularity, standardisation of components and ease of disassembly.
These criteria not only extend the life of products, but also facilitate their recycling when reuse is not an option.
In this context, spare parts from the circular economy play a key role: their recovery and reconditioning extend the life of products while reducing the demand for new resources.
Recycling, for its part, relies on advanced technologies. Molecular separation and purification processes enable recovered materials to be treated efficiently.
In addition, over-cycling, a technique for improving the properties of recycled materials, is increasingly used to create new high-quality products or components from previously rejected materials.
Ecodesign: a global strategic approach
Ecodesign is an integrated approach in which companies design their products with every phase of the product life cycle in mind, including end-of-life. This makes it possible to :
- Minimise the environmental impact of products by using resources wisely and reducing premature or final waste.
- Improve energy efficiency and reduce carbon emissions throughout the life of the product.
- Reduce production costs by choosing more durable and easily repairable materials.
Conclusion: A new industrial model
Maximising the second life of products is much more than just a trend.
It is a strategy for industrial transformation that offers numerous benefits: reduced production costs, minimised environmental impact, the creation of new business models and compliance with growing regulatory requirements.
Companies that proactively adopt these practices position themselves advantageously in the circular economy, creating a lever for growth and sustainable innovation.